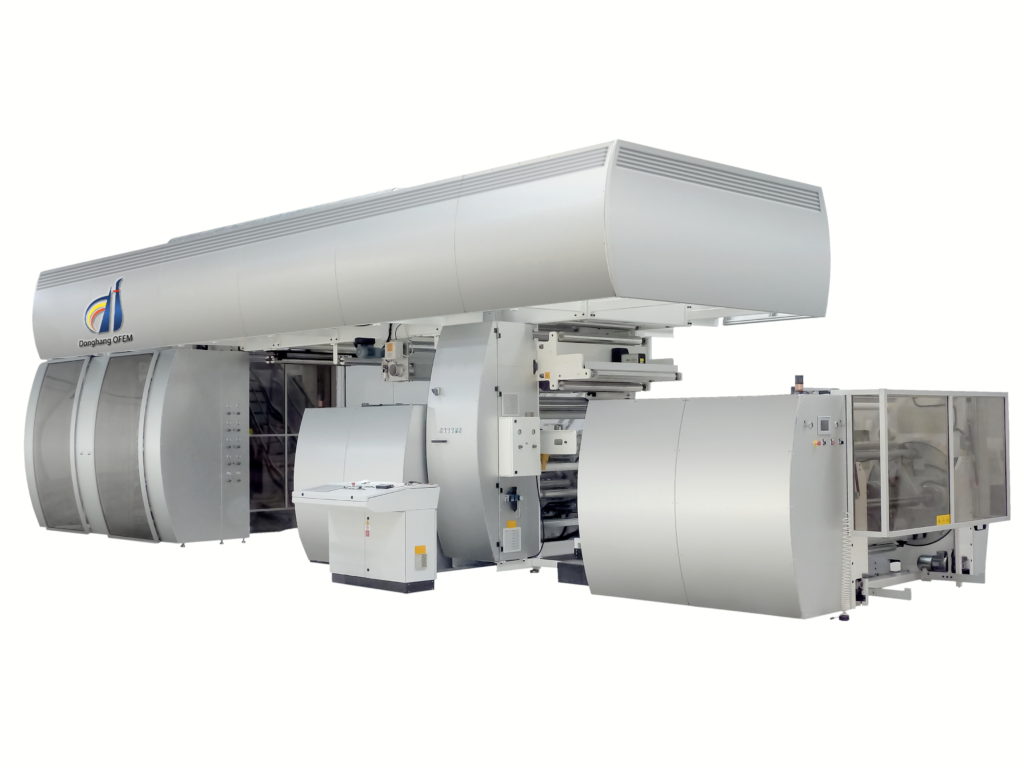
Recently, CI Flexo Tech organized a salon with subject how to improve CI flexo machine production efficiency. 8 leading printing companies who use CI flexo press provided data for their job, including effective working hour (printing, job change, commissioning), idle time (fault, maintenance, blade change), order, output, speed etc. After analysis all these data, it is found the their efficiency is only about 30%–65%. Far more lower than gravure printing (around 90%) and abroad printing company who use CI (around 75%–80%) This a big problem, it means some machine can at a very low efficiency and many time and money is wasted.Profitability of same machine in different printing house can be 2 times different.
According to these data, it has been found there three main factors impact machine efficiency, respectively job change & commissioning, abnormal machine stop,running speed lower than machine design speed. In order to improve efficiency, following suggestion are offered by professionals:
Job change & commissioning:
- Plate mounting. More training is needed and to setup standard mounting procedures.
- Pressure setting. Should do more test and data collection to find the best pressure curve for the machine. Shorten pressure set up time.
- Register setting. Plate mounting accuracy is critical to register. Meanwhile, regular maintenance for machine and sleeve is required to make sure machine can correctly find its zero position.
- Color setting. Should work closely with anilox roller and ink supplier. Try to find correct ink adjustment method and make sure get correct color within 2 time adjustment.
Abnormal machine stop:
- Printing substrate quality. Should make sure substrate has good quality and clean surface. Install necessary cleaning equipment to eliminate surface dust.
- Plate management. Choose correct plate making technology and equipment. Setup plate life management procedure, do proper clean and drying after job.
- Anilox roller management. Setup anilox roller portfolio. Try to avoid to have too many different specification anilox roller and do regular maintenance.
- Ink management. Setup color portfolio. make sure the ink has good printability and proper drying character.
- Testing plate. Should do system testing with testing plate every year to make sure all parameters are in correct range.
Running speed lower than machine design speed. this is more complex as it is related to all the things mentioned before. Basic idea is if everything are correctly setting, the running should be close to design speed. But we also need to take operator skill and job character。