Key points for water-based ink on flexo printing equipment
At present, the implementation of water-based printing is mainly aimed at the transformation of existing solvent-based ink production systems. Therefore, it is unrealistic to hope that a revolutionary and perfect technology will emerge in a certain link. It must require close cooperation in several industrial sectors.
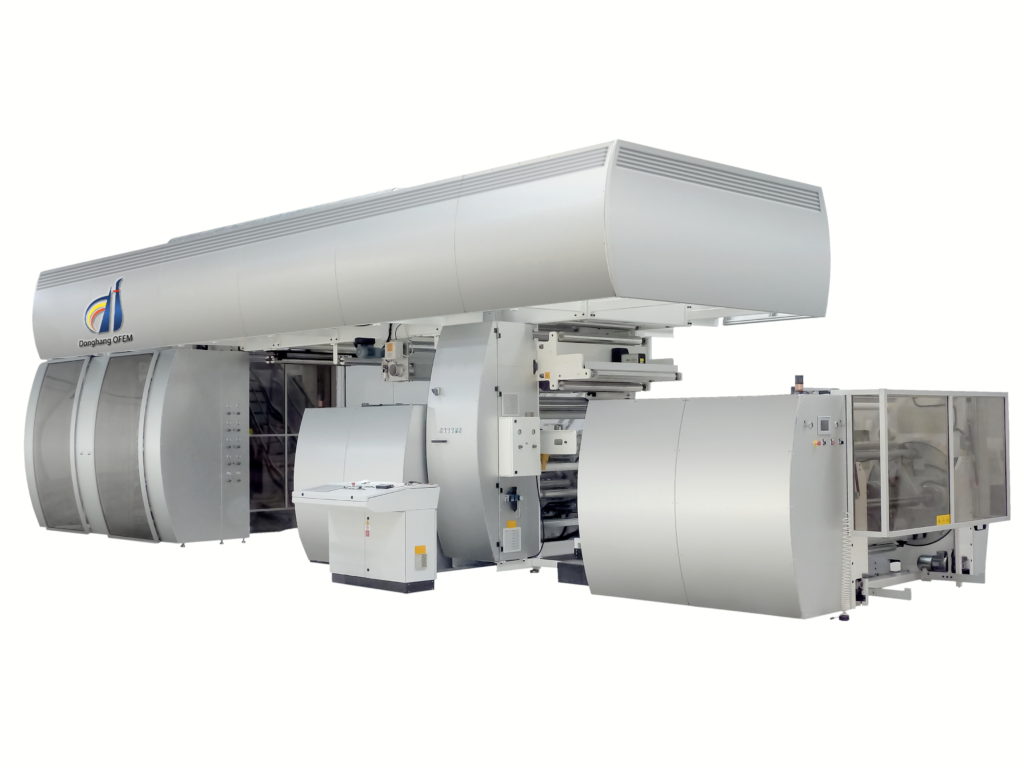
Substrates, inks, plate making and design, printing and processing are interrelated and influential. At the same time, some basic concepts, such as the use of thin ink layer printing methods, have been widely discussed.
The most important difference between the gravure printing machine and the flexo printing equipment is the length and transfer mode of the ink path (direct or indirect transfer). The flexo printing has one more anilox roller that transfers the ink in the middle than the gravure printing. Secondary distribution of ink volume (the way the ink on the flexographic anilox roll is transferred to the surface of the printing plate is substantially equivalent to the ink transfer of the gravure printing, both having an ink transfer rate of approximately 50%; the ink on the surface of the flexographic printing plate passes again The transfer can reach the surface of the substrate, and there is also about 40%-50% ink transfer rate), that is, the flexographic ink layer is thinner than the gravure.
The thinning of the ink layer is crucial for aqueous printing, which can greatly alleviate the drying problems caused by water-based inks.
We use at least 70% of the volatile components (residues of resins, pigments and auxiliaries) in water-based inks, usually consisting of water, alcohol/ether solvents and a small amount of VOCs such as amines. Simple framed 5% VOCs and 65% water. Therefore, the first element of water-based printing is to improve the drying performance of the ink. As an engineering method, it basically revolves around the four elements of water evaporation (temperature, dry area, air flow speed and humidity), such as increasing the temperature of the substrate (ink, ink, oven), increasing the drying area (the length of the oven) and accelerating the air velocity (wind speed and Air volume), reduce humidity (environmental dehumidification or oven dehumidification).
But the most important thing is to print the thin ink layer. This is the source control. Simply put, if water is the slowest drying material in the ink, then we only need to reduce the total amount of water, and other slow. The same is true for dry volatiles, as long as the amount of ink is reduced, the drying process is relatively accelerated.
Therefore, the printing method of the flexographic plate is especially recommended, and it is recommended to increase the number of anilox lpi.
DH (Donghang graphic) is a professional manufacturer for flexo printing equipment in China and has been in this industry for over 20 years. DH has more than 800 flexo printing equipment installed and products covers inline and CI flexographic printing equipment. More information, please visit www.dhflexoprinting.com