Basic composition of water-based ink
Aqueous inks generally consist of pigments, water soluble or water dispersible resins, neat water and small amounts of ethanol and auxiliaries. The pigment used in the aqueous ink is mainly an organic or inorganic pigment which is strong in alkali resistance and has good dispersibility in an aqueous system. The organic pigment has a small specific gravity, a high coloring concentration, and a bright color; the inorganic pigment has a large specific gravity, and the color density is weaker than that of the organic pigment, but is relatively stable. In addition, some water-based inks also use dyes. In the process of water-based ink manufacturing, the pigment achieves a balance between mutual attraction and mutual exclusion of pigment particles through wetting, dispersing, and stabilizing. Pigments not only determine the coloration phase and color saturation in aqueous inks, but also have a significant impact on many physical properties and even storage stability.
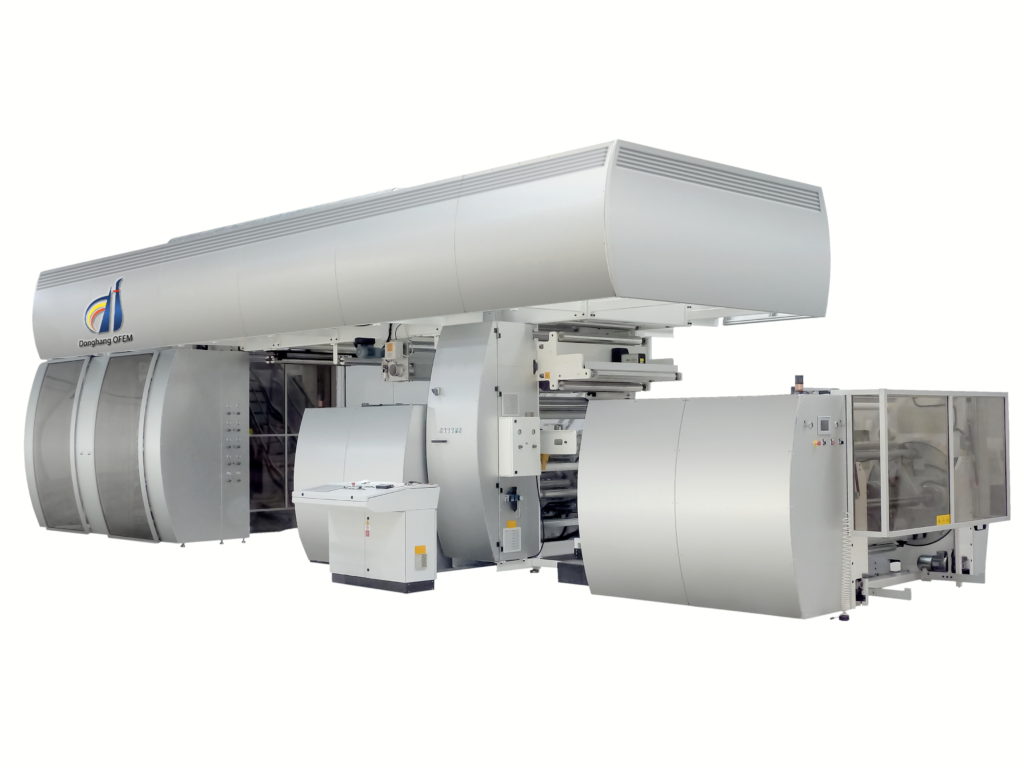
more DH flexo press machine: please visit here.
Water-based ink binders are mainly water-soluble or water-dispersible resins, which are important factors affecting the quality of water-based inks, especially high-precision water-based inks. There are many types of water-based resins, such as maleic acid-modified rosin resins, water-soluble acrylic resins, styrene maleic acid copolymer resins, aqueous polyester resins, waterborne polyurethane resins, aqueous amino resins, and polyvinyl alcohol and methyl cellulose. Wait.
The principle of water solubility is that these polymer resins generally contain: -COOH (carboxyl), -OH (hydroxyl), -NH2 (amine) and other hydrophilic groups, which can be completely processed after a certain process. Water soluble resin. The viscosity, adhesion, gloss, drying performance, and printability of the aqueous ink mainly depend on the aqueous resin binder.
Since the water-soluble acrylic copolymer resin has significant advantages in terms of gloss, weather resistance, heat resistance, water resistance, chemical resistance and stain resistance, it is possible to obtain a resin having different characteristics by using appropriate monomer copolymerization, so It is widely used in water-based inks and water-based coatings at home and abroad.
The solvent for aqueous inks is mainly pure water, in addition to a small amount of ethanol, cosolvents and various additives.
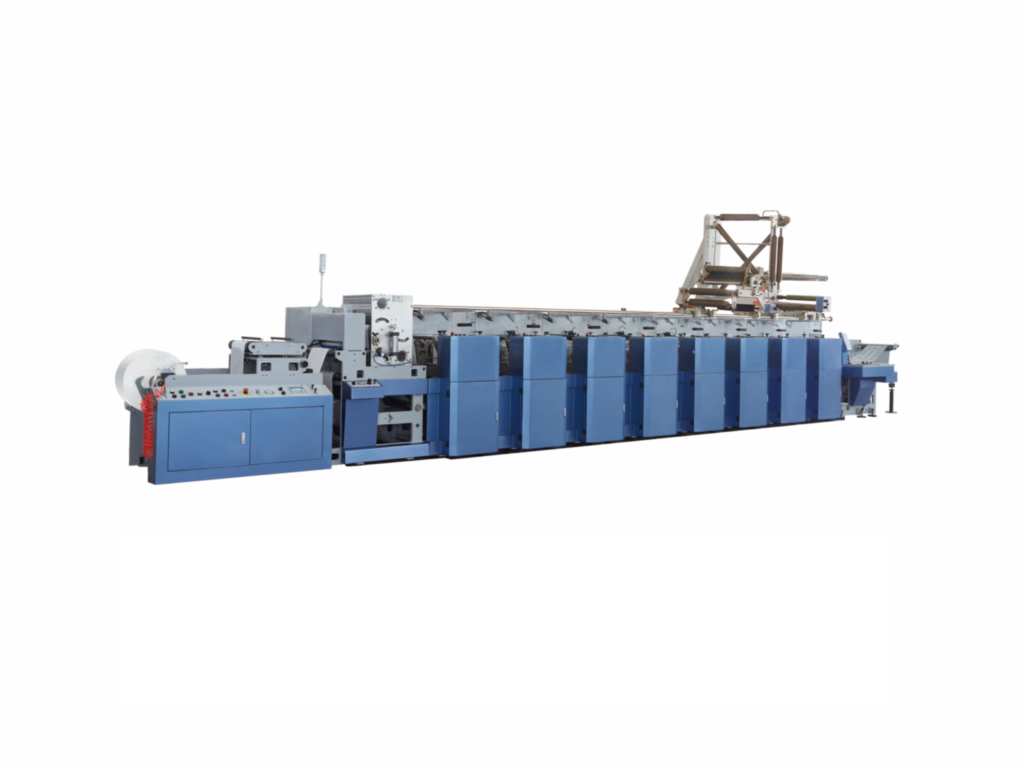
Water-based ink application
Whether the application of water-based inks is appropriate is an important factor in whether water-based inks can be printed normally and affect print quality. Since the ink transfer principle of flexo-printed water ink is completely different from traditional offset printing and embossing, the application of water-based ink cannot be guided by the traditional ink concept. The application of water-based inks must understand the characteristics and requirements of the flexographic process and flexo press machine. It is necessary to understand the selection and use of water-based ink additives. It is necessary to master the control and adjustment of the viscosity and pH of water-based inks.
Flexo printing refers to the printing method of transferring ink through an anilox roll using a flexographic plate (including a rubber plate, a photosensitive resin plate). The composition and application of water-based inks must be adapted to the special requirements of the two components of flexographic printing, such as flexible plates and anilox rolls.
Flexible version
The flexographic version has a solvent resistance problem whether it is a rubber or a photosensitive resin. For inks and cleaning agents for flexo printing, solvents must first be selected that will not cause erosion of the flexographic plate.
2. Anilox roller
At present, high-end flexo printing machines use laser-engraved ceramic anilox rolls, which is the heart of flexo printing and one of the important features of today’s flexo printing.
The anilox roller is an important task in the flexo printing to transfer and control the amount of ink. Therefore, the number of lines of the anilox roller must be selected according to the condition of the product. In general color printing, the solid printing generally selects an anilox roller of about 400 LPI, the ink layer is relatively full and thick, and the fine layered version of 150 LPI is printed, and an anilox roller of 700 LPI or more is required. The number of screen lines of the anilox roller is generally 4-6 times that of the number of printed lines, so that the printed matter can obtain better definition and resolution.
Keeping the anilox roller clean and completely removing the blockages in the cell (such as dry ink, resin and dust) is an important part of ensuring high-quality printing of the flexographic plate. The mesh is clogged, causing the ink transfer volume of the anilox roller to decrease, which is an important cause of light ink color, uneven ink color, and insufficient ink volume, and must be paid enough attention.
Water-based inks can be cleaned with tap water before they are wet, ie, they are not dry. However, there is nothing to do with the dried aqueous ink tap water. It must be cleaned with an aqueous ink cleaner. In order to completely remove the deposits in the cells, it should be brushed with a very fine stainless steel wire brush.
In addition to timely cleaning every time, it should be thoroughly inspected and cleaned regularly. In addition to the usual chemical cleaning methods, the anilox roller cleaning method includes an ultrasonic cleaning method and a low pressure spraying method.
Flexographic ink-based ink control indicators
Flexo ink should have better fluidity and proper viscosity, proper drying speed and good adhesion to substrate. In addition, the material in the aqueous ink does not affect the flexographic plate and the rubber roller, does not have an odor after drying, and has good storage stability. After the aqueous ink has been stored for a long period of time, it will be re-dispersed after being stirred and precipitated.
The control indicators for flexographic aqueous inks mainly include viscosity, fineness, drying speed and pH.
1. Viscosity control and adjustment
Viscosity is a property that prevents fluid flow and is a measure of the interaction of fluid molecules to create a resistance to the relative motion of their molecules, ie the resistance of fluid flow. Viscosity is the primary control indicator for aqueous ink applications because it directly affects the transfer properties of the ink and the quality of the flexographic print. The viscosity is related to the viscosity and density of the resin in the binder, as well as the type and particle size of the pigment (pigment or dye).
In printing, the ink with low viscosity shifts quickly, which causes defects such as light color, large dot enlargement value, high-light dot deformation, and uneven ink transfer. The slow transfer of high viscosity ink will affect the performance of the anilox roller transfer ink. , resulting in uneven ink color, sometimes not printed color and dirty, paste and other defects.
The viscosity is low and can be adjusted by mixing with new ink. When the viscosity is high, it can be diluted with water or a mixture of water and ethanol (50% each), or it can be adjusted with an aqueous ink stabilizer.
In addition, during the printing process, the temperature also has a large influence on the viscosity of the ink, and generally the viscosity rises as the temperature rises, and vice versa, the viscosity increases. Therefore, in order to keep the print color consistent during the printing process, the temperature of the printing shop should be kept as constant as possible.
From the domestic use situation, the viscosity of the water-based ink used in the satellite flexo printing machine is generally controlled at 15 seconds to 30 seconds (@25 ° C, measured by the Zahn 2# cup). Of course, the viscosity selection is also required. Depending on the condition of the substrate (eg paper, aluminum, plastic, etc.) and the type and speed of the equipment, the faster the speed, the smaller the viscosity should be.
The viscosity adjustment of the aqueous ink before the machine can be used as a special diluent for aqueous ink, and the viscosity adjustment of the printing process requires the use of an aqueous ink stabilizer.
2. Fineness
The fineness of the ink means the degree to which the solid matter such as a pigment or a filler mixed in the linked group is dispersed. The fineness of the ink is also an important quality indicator because it is not only related to the application properties of the ink (including tinting strength, hue, stability, etc.), but also to the rheological properties and economic benefits of the ink.
In the actual printing, different fineness of ink can be selected according to specific requirements. When the printing network is relatively thin and the precision is relatively high, the fineness of the ink is relatively high; when the printing is not very high precision printing or solid printing, the fineness of the ink can be appropriately reduced.
3. Application of additives
Due to the different requirements of printed products, the nature and quality of the substrates, and the different speeds of printing and drying, the performance requirements for water-based inks are also different.
A water-based ink often cannot meet and adapt to various requirements. Therefore, it is necessary to develop a variety of water-based inks to adapt to different special requirements, and the application of various water-based ink additives can also adjust and meet certain different needs. .
The application of water-based ink additives can improve the printing suitability of water-based inks and ensure the smooth progress of the printing process. In the printing process, the viscosity and pH of the solvent, such as amine, water and ethanol, will become unstable, the viscosity will increase, the pH will decrease, and the printing suitability will be affected. Waterborne ink additives are often adjusted. Commonly used aqueous ink additives include:
1) Stabilizer
The binder used in the aqueous ink is mainly an alkali-soluble acidic resin, so the control of pH is very important. In addition to metallic inks, the pH of aqueous inks should generally be controlled at 8.5 to 9.5, which is slightly alkaline. At this time, the water-based ink has the best printing performance and the printing quality is the most stable.
Since the amine will volatilize during the printing process, the operator will add new ink and various additives from time to time, so the pH of the ink changes at any time. When the pH of the aqueous ink is higher than 9.5, the alkalinity is too strong, the viscosity of the aqueous ink is lowered, the drying speed is slowed, and the water resistance is deteriorated; when the pH is lower than 8.5, the alkalinity is too weak, and the aqueous ink is The viscosity will increase, causing the drying speed to become faster, which may easily block the printing plate and the anilox roll, cause dirty plates, and generate bubbles.
Since the influence of pH is directly related to the viscosity, it is recommended to control the two in actual printing, especially in the case of color printing. In addition to the viscosity cup, a simple pH meter (see Figure 1) should be prepared for testing at any time. When the pH of the aqueous ink is low, a pH stabilizer or a small amount of alkaline substance may be added. When the pH is high, a solvent or a diluent may be added for dilution.
Figure 1 pH meter
2) slow drying agent
Slow-drying agents inhibit and reduce the drying speed of aqueous inks, prevent surface crusts, reduce paste, and improve print clarity. It can be used as needed, generally not more than 3% at a time.
3) Dilution agent
The thinner can be used to lighten the color, but does not reduce the viscosity and drying speed. The thinner is also an aqueous brightener, which can improve the brightness of the aqueous ink. It should be used as needed.
4) Defoamer
Bubbles in aqueous inks can be suppressed and eliminated. Generally, the amount added is not more than 1%. When the viscosity of the aqueous ink is too large and the water is too much, it is easy to foam. Therefore, the viscosity of the aqueous ink should be adjusted to the normal range first, and then the defoaming agent is added. The effect is very obvious.
5) Water-based ink cleaner
The aqueous ink cleaner is generally a concentrate, which is diluted and mixed with 2-5 times of water when used. It is mainly used for cleaning flexographic plates, anilox rolls and ink rollers, and is very effective for cleaning dry inks.