1. effectiveness
CI flexo printing machine speed is fast, the current mainstream models are as high as 350 ~ 500m / min, which is unmatched by the gravure printing speed of 120 ~ 200m / min when printing soft and stretchable film.
2. Register accuracy
The gravure printing path is long, and the color per color is 4 to 6 m, and the distance between the color groups of the ci flexo printing machine is only 40 to 60 cm. Gravure often encounters problems with lateral register, and the wider the printed web, the more inaccurate the lateral register, especially for soft, stretchable film materials.
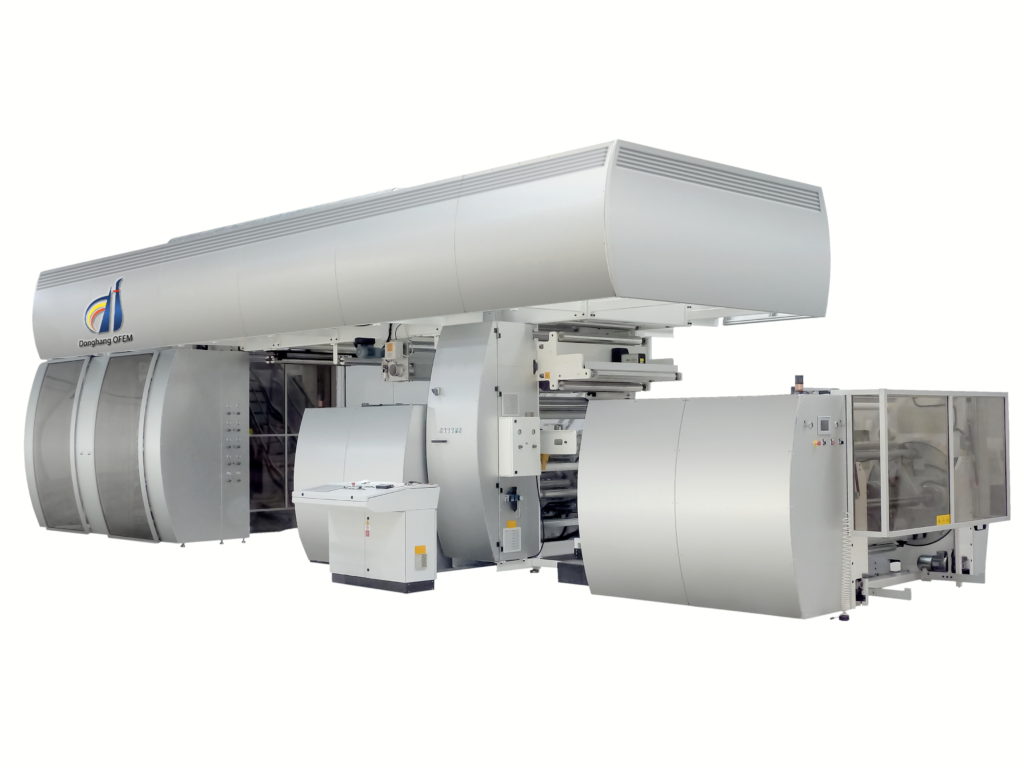
Taking soft LDPE film products as an example, the yield of flexo printing is about 5% to 10% higher than that of gravure printing; and the color registration accuracy of flexo printing is as high as 0.1 to 0.2 mm, and the high-end printing presses can achieve higher overprinting precision.
This is particularly evident when printing breathable film. Since the breathable film is easy to stretch, the thickness is only 12-20 g/m2, and high-speed, wide-width printing cannot be achieved by gravure printing. Therefore, a large number of multi-color printed breathable films are currently available by flexo printing.
3. Energy consumption
Whether using steam or electricity for drying, the cost of flexo printing is lower than that of gravure printing. And the power cost required for the press to run is also lower than the gravure.
4. Ink and solvent consumption
The flexo ink layer is thinner than the gravure, so the ink consumption is less than the gravure.
In addition, because flexo printing uses closed ink chamber and closed ink circulation system, solvent evaporation can be greatly reduced. Compared with gravure open ink tank, flexo solvent consumption is 40% to 50% lower than gravure printing. .
Regardless of the difference in the width of the printed door, the output of a stable operation of the gravure press and flexo press is about 40 million meters per year. With an average width of 800 mm, it can produce 32 million m2 of products per year. flexo printing can reduce the emission of 61.375Kg solvent (including solvent consumption and solvent contained in the ink) to the atmosphere per gm2, so that one flexo printing machine can discharge less than one year compared with the gravure printing machine. The solvent is 196.4 tons, so it is the main reason why flexo printing is an environmentally friendly printing method.
The flexographic solvent is mainly ethanol or n-propanol, or an aqueous solvent. The gravure solvent contains a large amount of isopropanol, ethyl acetate and n-propyl acetate. It is obvious that even the same emission is more environmentally friendly.
5. Job change efficiency
The gravure printing machine replaces an 8-color product, which takes about 1.5 to 2 hours and consumes 200 to 300 m of film.
The flexo press replaces an 8-color product. The gear-driven CI flexo press takes 2 to 3 hours. The gearless servo-driven satellite flexo press takes 0.75 to 1.5 hours and consumes 80 to 100 m of film. The latest flexo press with automatic cleaning ink system and automatic pressure control system takes only 0.5 hours or even less.
6. Consumables consumption
Gravure uses a heavy-pressure, co-directional single-squeegee system that uses a light-pressure, forward-reverse double-squeegee system that consumes approximately 30% of the gravure.